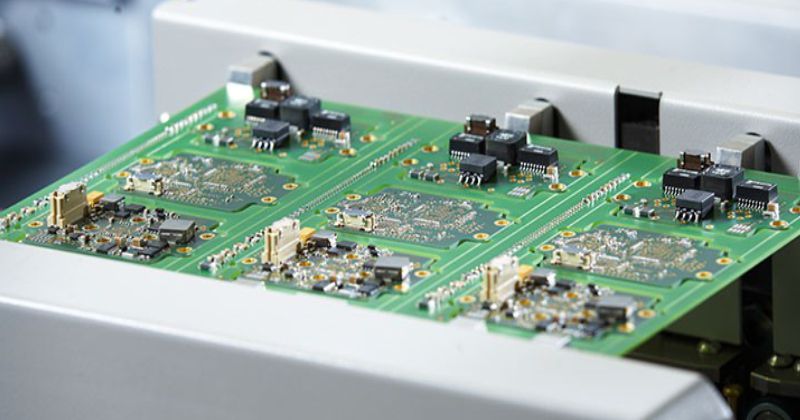
SMT Technology & Process
PCB manufacturing utilizes the SMT process in modern times. It stands for Surface-Mounted technology. As the name implies, this technology works by mounting components onto a bare PCB.
The reason that this technology is so important is because it provides a variety of advancement. Now, PCB can be much smaller because of the SMT process. This is usually automatic, where previous PCBs were mostly handcrafted, which saves everyone time and money.
Benefits of Surface Mount Technology
The surface mount technology (SMT) of printed circuit board (PCB) assembly was introduced in 80s. In this technology, the components are mounted directly onto the surface of the electronic board. Ever since this technology was introduced, it was well-accepted in the PCB manufacturing industries due to its simple and effective application. Owing to a wide range of benefits offered by surface mount technology, it quickly overtook the through-hole technology of PCB assembly in significant areas. The following points discuss why SMT is popular and why this technology is a standard adoption in PCB assembly.
Why is SMT Popular?
Component Mounting: In recent times, the component sizes are getting smaller by day as the PCB design requirements call for being compact. Due to which, the component sizes are being reduced by over 60-90%. In these conditions, the conventional through-hole assembly technology(THT) occupies more space in the PCB. But the surface mount technology(SMT) mounts the components on the surface itself, miniaturization of a component does not affect the PCB assembly and in fact optimizes the overall process. Therefore, the smart PCB designs can be opted for using the SMT component mounting.
Machine Compatible: SMT components are highly compatible with automation processes. The proceedings like design standardization, component serialization, pick-and-place mounting, and soldering, etc can all be automated in the SMT.
Production Efficiency: The efficiency of production increases due to less manual involvement and equipment switching time is also reduced. Using the right and powerful pick & place machine can however accelerate the complete process.
Material Cost Reduction: SMT requires no material removal from the board, therefore scrap material reduction takes place. Also, SMT reduces the consumption of packaging material. Reduction in the cost of raw material and packaging material eventually reduces the material costs.
Easy Mounting Process: SMT features easy pick-and-place component mounting, therefore, the overall complexity of the process is minimized.
Reduced Radio Frequency Effect: Surface-mounted components have short leads or no leads, so the distribution in the electronic circuit is reduced due to which the radio frequency effect is less in surface mounted PCBs.
High Speed Signal: The surface mount technology is commonly utilized for high-density PCBs. These boards may feature 4 to 20 joints or more per square centimeter. Due to these highly and densely populated components, there are short circuits that reduce any transmission delays. Therefore, high transmission speed is offered by surface mounted boards.
With several years of experience, we have the right equipment, resources, and engineering expertise to produce PCB Assembly. You can call Auckam or email to mail@auckam.com today to discuss your requirements.